Fasteners and Machining: Enhancing Layout for Superior Manufacturing
Grasping the Art of Bolts and Machining: Technologies and Ideal Practices
In the world of commercial manufacturing and design, the mastery of bolts and machining is a keystone of making sure architectural stability, performance, and longevity in numerous applications. Join us as we explore the latest improvements and dig into the nuanced world of understanding bolts and machining, uncovering crucial understandings and methods that can elevate your strategy to design remedies.
Development of Attachment Technologies
Throughout the industrial change and into the modern-day period, the development of attaching innovations has actually been noted by continual improvements in performance and reliability. Bolts, such as rivets, bolts, and screws, play an important duty in different sectors, including automobile, aerospace, construction, and electronic devices. The requirement for more powerful, much more long lasting, and easier-to-install fastening solutions has driven development in the area.
One substantial advancement has actually been the shift towards precision machining methods to create fasteners with higher resistances and remarkable performance. This change has actually made it possible for makers to generate bolts that meet stringent top quality standards and offer increased resistance to deterioration and fatigue.
Furthermore, the introduction of innovative products, such as titanium alloys and compounds, has actually reinvented the abilities of bolts. Fasteners and Machining. These materials give outstanding strength-to-weight proportions, making them ideal for applications where decreasing weight is crucial without endangering architectural integrity
Improvements in Machining Approaches
In the realm of industrial production, the continuous development of machining methods has actually led the means for extraordinary precision and efficiency in the production of bolts. One of the considerable improvements in machining approaches is the application of Computer system Numerical Control (CNC) technology. CNC makers offer unrivaled precision and repeatability by permitting automated control of machining tools. This precise control allows producers to produce complex and elaborate bolt designs effortlessly.

Additionally, the fostering of multi-axis machining centers has allowed simultaneous cutting operations from numerous angles, additionally improving efficiency and reducing production times. By utilizing these advanced machining approaches, producers can meet the raising demand for top notch fasteners while maintaining cost-effectiveness in their operations.
Picking the Right Fastener Materials
Picking the suitable material for bolts is a crucial decision that substantially influences the efficiency and durability of the constructed components. When picking the appropriate fastener material, several elements need to be considered to ensure the longevity and integrity of the last item. The material picked need to be suitable with the ecological conditions the fasteners will certainly be exposed to, such as temperature variations, wetness degrees, and corrosive aspects.
Usual products made use of for fasteners consist of stainless-steel, carbon here steel, titanium, and light weight see here aluminum, each offering distinct residential properties that match various applications. Stainless steel, for example, is known for its deterioration resistance, making it perfect for outdoor or aquatic atmospheres. Carbon steel is an affordable choice appropriate for numerous general-purpose applications. Light weight aluminum is lightweight and often used in markets where weight is a vital variable. Titanium, on the other hand, is corrosion-resistant and extremely strong, making it appropriate for high-performance applications.
Enhancing Accuracy in Machining
Accomplishing ideal precision in machining is necessary for making sure the top quality and efficiency of machined parts. Precision in machining describes the capability to constantly generate components within limited resistances and with high accuracy. To improve accuracy in machining, suppliers use a selection of advanced techniques and technologies. One secret approach is utilizing Computer Numerical Control (CNC) equipments, which supply superior precision and repeatability contrasted to conventional manual machining techniques. CNC equipments are programmable and can execute intricate machining operations with minimal human intervention, causing greater precision degrees.
In enhancement to CNC machining, using innovative cutting devices and device holders can additionally dramatically enhance precision. Premium cutting devices with advanced finishes minimize rubbing and wear, leading to a lot more exact cuts and dimensional precision. Furthermore, executing stringent quality assurance procedures throughout the machining process, such as normal examinations and calibration of equipment, aids maintain regular precision levels. By prioritizing precision in machining, suppliers can achieve premium item high quality, tighter resistances, and improved total efficiency of machined elements. see here now
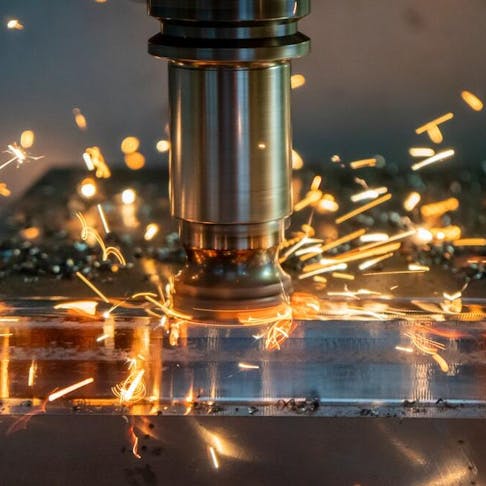
Ideal Practices for Bolt Installment
Precision in machining plays a critical function in ensuring the integrity and long life of fastener installments. When it involves finest methods for fastener setup, one key facet is the correct selection of fasteners based on the particular application requirements. Using the correct type, size, and material of bolt is vital to guarantee ideal performance and longevity. Fasteners and Machining. Additionally, it is extremely important to adhere to producer guidelines and recommended torque worths during the setup process to stop over-tightening or under-tightening, which can bring about premature bolt failing.
In addition, making certain that the fastener strings are clean and totally free of particles before installation is vital to achieving a secure and effective link. By sticking to these best practices, suppliers can optimize the stability and efficiency of their fastener installments.
Final Thought
To conclude, the advancement of securing innovations and developments in machining techniques have actually considerably enhanced the efficiency and effectiveness of bolt installation processes. By picking the appropriate bolt products and enhancing precision in machining, producers can attain ideal results in their operations. Adhering to finest techniques for fastener setup is crucial in guaranteeing the sturdiness and integrity of settings up. In general, mastering the art of fasteners and machining includes continuous advancement and adherence to ideal methods.
In the realm of commercial production, the continuous development of machining methods has led the way for unprecedented accuracy and efficiency in the production of fasteners.Precision in machining plays an important function in ensuring the reliability and durability of bolt setups. When it comes to ideal techniques for bolt installment, one essential facet is the proper selection of bolts based on the specific application demands. By selecting the best bolt products and improving accuracy in machining, producers can achieve ideal results in their operations. Generally, understanding the art of bolts and machining entails constant development and adherence to ideal practices.